NepTech’s services to enhance your vessels’ performance
From the preliminary design phase to sea trials, NepTech provides advanced methodologies in CFD simulations (Computational Fluid Dynamics) to accurately model complex naval hydrodynamics phenomena while ensuring reliable predictions
Drag resistance and propulsion
Predicting a vessel’s resistance to forward motion is a key step in assessing energy performance. It enables the optimization of propulsion system design and energy consumption from the earliest stages of preliminary design.
Service offer
1. Analysis of drag resistance
- Resistance in calm water
- Added resistances:
○ Appendages
○ Propulsors
○ Surface roughness
2. Propulsive performance calculation
- Propulsive coefficients (wake fraction and thrust deduction)
- Hydrodynamic impact of appendages (rudder, daggerboard, etc.) and other potential disruptors
3. Specific studies and analyses
- Comparative studies of different vessel designs
- Hydrodynamic polar diagrams
- Recommendations for improving the design of hulls
Seakeaping
Seakeeping simulations are essential for predicting vessel behavior, assessing compliance with stability, comfort, and safety criteria, and estimating the impact of waves on energy consumption under real or extreme maritime conditions.
Service offer
1. Analysis of hydrodynamic resistance
Hydrofoils
NepTech stands out for its expertise in hydrofoil design and the development of advanced methods for sizing and validating the performance of foil-equipped vessels, whether flying or non-flying.
Service offer
NepTech provides a proven iterative sizing process:
- Conceptual study
- Preliminary sizing (analytical methods)
- Performance validation:
○ CFD simulations of standalone hydrofoils
○ CFD simulations with the vessel
Aerodynamics
Aerodynamics play a crucial role in assessing vessel performance. Aerodynamic simulations aim primarily to determine the drag coefficient of the above-water structure, in order to evaluate the wind’s impact on overall performance.
Service offer
1. Analysis of aerodynamic resistance
- Aerodynamic resistance
- Performance under real wind conditions
- Added resistances:
○ Generated by superstructures
○ Due to surface roughness
2. Specific studies and analyses
- Comparative design studies
- Aerodynamic polar diagrams
- Recommendations for improving the design of above-water structures
- Study of recirculation zones, flow separation, and vortices
A project?
neptech’s technical team
supports your projects
Innovations in numerical modeling
Air lubrification
Air lubrication simulation for hulls in CFD is a complex process that involves the qualification of multiphase models (water + air), while optimizing calculation efficiency.
To meet the challenge of ensuring the performance of ALS (Air Lubrication System) technologies, NepTech collaborates closely with its technical and academic partners.
Drag resistance in shallow water
Shallow depths in coastal and river areas significantly impact the energy consumption of vessels. To address this, NepTech develops advanced CFD methods to simulate forward resistance in shallow water.
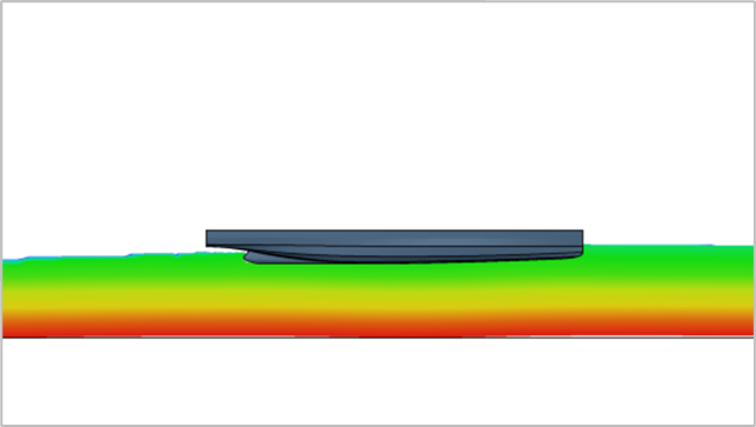
These complex phenomena are studied for all types of vessels, with a particular focus on the specificities of catamarans.
NepTech’s ambition is to develop precise and rapid methodologies that allow the integration of these physical phenomena from the early stages of vessel design.
A QUESTION?
schedule a meeting with
our technical team
Validation cases
NepTech compares its numerical simulations with experimental validation cases (standardized and referenced) in order to demonstrate the predictive capacity of the CFD methodologies developed
This approach demonstrates the accuracy, credibility, robustness and continuous improvement of our numerical tools
Validation of the overset meshing method
This report presents a comprehensive validation study of the overset meshing method using NepTech’s digital testing basin.
Analysis of different resolution methods for planing hulls
This report presents a comprehensive study on the influence of meshing strategies and numerical parameters on the accuracy and efficiency for planning hulls.
Calm water: Generic Prismatic Planing Hull (GPPH), Naval Surface Warfare Center
This benchmark provides a comprehensive validation study on the Generic Prismatic Planing Hull (GPPH) in calm water, using NepTech’s digital towing tank.
Calm water: Series 60 (monohull and catamarans)
This benchmark provides a comprehensive validation study on the Series 60 catamaran in calm water, using NepTech’s
digital towing tank.
Calm water: DELFT 372 catamaran, Delft University of Technology
This benchmark provides a comprehensive validation study on the DELFT 372 catamaran in calm water, using NepTech’s digital towing tank.
Calm water: KRISO Container Ship (KCS), Tokyo 2015 Workshop
This benchmark provides a comprehensive validation study on the KRISO Container Ship in calm water, conducted as part of the Tokyo 2015 Workshop on CFD Ship Hydrodynamics, using NepTech’s digital towing tank.