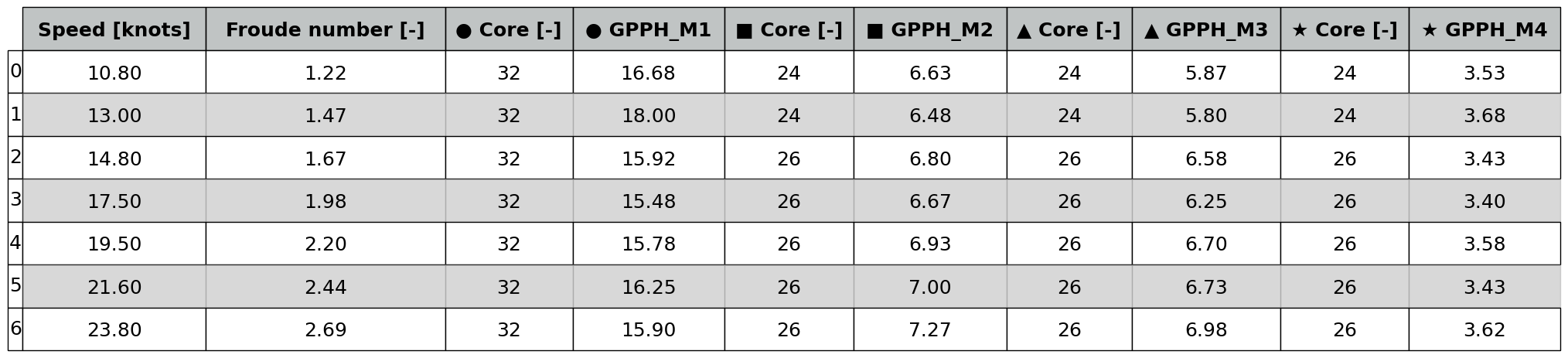
This report presents a comprehensive study on the influence of meshing strategies and numerical parameters on the accuracy and efficiency of CFD simulations for planning hulls, using NepTech’s digital testing basin. The study focuses on a high-speed regime, covering a Froude number range from 1.2 to 2.7, based on GPPH. The analysis compares four different approaches, showing that the most accurate setup provides highly precise results, while a faster alternative allows for efficient design exploration with a slight trade-off in accuracy.
For resistance predictions, method M2 stands out as the most precise across all speeds, making it the preferred choice when accuracy is the priority. Similarly, M1 and M2 provide the best results for dynamic pitch, while all methods perform similarly for dynamic heave. However, when fast turnaround times are required, such as for design space exploration, method M4 offers a significantly reduced computational cost with only a slight loss in accuracy.
Beyond accuracy, computational efficiency is a critical factor in simulation performance. The study highlights a significant reduction in computation time, ultimately reaching a duration between 3 and 4 hours. Approximately 4.4 to 4.9 times faster than the initial simulation setup. Given that method M1 was already optimized compared to standard practices, the actual time savings are even more substantial. The most effective strategies for improving computational performance are the implementation of a mesh deformation approach and the removal of the acceleration ramp.
Overall, this study demonstrates that careful selection of meshing strategies and numerical parameters can achieve both high accuracy and computational efficiency in CFD simulations of planning hulls. Method M2 emerges as a strong candidate for future simulations, striking an optimal balance between precision and reduced computational cost.
Despite these optimizations, the overset method remains a valuable tool. An inaccurately pre-estimated equilibrium state that deviates too far from the dynamic one can lead to simulation instabilities in methods M2, M3, and M4. Therefore, validating all four methods was essential to ensure adaptability to different project requirements.
All these best practices and methodological improvements have been integrated into NepTech’s digital towing tank, ensuring high-fidelity simulations tailored to the specific needs of naval architecture and hydrodynamic design.
Recent Comments